The positioning accuracy of CNC machine tools directly affects the machining accuracy of the machine tool. Traditionally, a stepper motor is used as a driving mechanism. Due to the inherent characteristics of the stepping motor, the repeatability of the machine tool can reach a pulse equivalent. However, the pulse equivalent of the stepping motor cannot be small, and thus the positioning accuracy is not high. The pulse equivalent of the servo system can be much smaller than that of the stepper motor system, but the positioning accuracy of the servo system is difficult to reach one pulse equivalent. Since the CPU performance has been greatly improved, the software can effectively improve the positioning accuracy. We analyze the reason that the conventional control algorithm leads to large error in the positioning accuracy of the servo system, and proposes a method of segmental linear deceleration and accurate positioning in open loop mode. It has achieved good results in practice.
First, the cause of the positioning error of the servo system and the way to overcome
Normally, the servo system control process is: speed up, constant speed, deceleration and low speed approaching the positioning point, the whole process is position closed loop control. The two processes of deceleration and low speed approaching the positioning point have a significant influence on the positioning accuracy of the servo system.
There are many implementation methods for deceleration control. Commonly used are exponential law acceleration and deceleration algorithms and linear law acceleration and deceleration algorithms. The exponential law acceleration/deceleration algorithm has strong tracking ability, but when the speed is large, the stationarity is poor, and it is generally applicable to the cutting process with higher tracking response requirements. The straight-line regular acceleration/deceleration algorithm has better stationarity and is suitable for use in a fast positioning mode with a large speed variation range.
When selecting the deceleration law, not only the stationarity should be considered, but also the positioning accuracy at the time of stopping is considered. In theory, as long as the deceleration point is selected correctly, the exponential law and the linear law deceleration can be accurately positioned, but the difficulty is the determination of the deceleration point. The usual methods for determining the deceleration point are:
(1) If the same acceleration/deceleration law is used during starting and stopping, the deceleration point can be determined according to the relevant parameters and symmetry of the speed increasing process.
(2) Calculate the deceleration point according to the parameters such as the feed speed, deceleration time and acceleration of deceleration. Under the condition that today's high-speed CPU is very popular, this is easy to implement for the CNC servo system, and the comparison method (1) flexible.
During servo control, the software judges in each sampling period: if the remaining total feed amount is greater than the remaining feed amount corresponding to the deceleration point, the instantaneous feed rate is constant (equal to the given value), otherwise, according to a certain rule slow down.
Theoretically, the remaining total feed is decelerated just equal to the remaining feed rate corresponding to the deceleration point, and decelerates to the stop point according to the expected deceleration law. But in fact, when the servo system is running normally, the number of pulses fed back in each sampling period is several, ten, dozens or even more, so the actual deceleration point does not coincide with the theoretical deceleration point. As shown in Figure 1, the maximum error is equal to the number of pulses in one sampling period before deceleration. If the actual deceleration point is advanced, the deceleration speed as expected will drop to a low point and the positioning point has not yet arrived, and it may take a long time to reach the positioning point. If the actual deceleration point lags behind the theoretical deceleration point, the speed is higher when the positioning point is reached, which affects the positioning accuracy and stability. To this end, we propose a piecewise linear deceleration method.
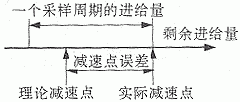
Figure 3 speed control block diagram
2, the principle of determining the parameters of several groups
(1) During the normal deceleration process of V0, V1 and V2, the position error of the deceleration point is compensated by the final low-speed approach phase, so that V0 is very difficult to select. If V0 is selected too small, it should be guaranteed that T0 ≥ (VG / V0), it takes a long time to reach the positioning point; if V0 is selected larger, it directly affects the positioning accuracy. Compared with the conventional deceleration method, the piecewise linear deceleration method increases the time periods of BC and DE, and the position error of the deceleration point can be mostly compensated at a higher speed. Therefore, V0 can be chosen to be small. The minimum speed of the servo system is usually available, which improves the positioning accuracy of the servo system. V1 and V2 can take 1% and 10% of the maximum speed of the servo system, respectively.
(2) The greater the acceleration of a1, a1 and a2, the shorter the deceleration process, but the greater the impact and error caused. Therefore, the acceleration in the high-speed phase may be larger to ensure the rapidity of the deceleration process; the lower acceleration phase should take a smaller acceleration to ensure the positioning accuracy. Usually the value of a1 is numerically equal to V0.
(3) T0, T1 and T2 According to the previous analysis, in order to compensate the position error of the deceleration point, T0=KV1/V0, T1=KV2/V1, T2=KVG/V2 should be taken, where K is the reliability coefficient. To compensate for the calculation error of the algorithm and the influence of other uncertain factors, K=1.1~1.3 is often taken.
This method has nothing to do with the characteristics of the servo system itself, and can be used as a deceleration control method for any servo system at any speed. In the numerical control system of the YKA7232 worm wheel grinding machine developed by Shanghai Machine Tool Plant, the control method of the piecewise linear deceleration open loop approaching the positioning point is adopted. The measured positioning accuracy and repeat positioning accuracy of each axis are controlled within one pulse equivalent, and the performance is stable, and good results are obtained.
PC Cable:MINI DIN,D-SUB,SCSI.The display connecting line includes the data cable connecting the host computer and the display screen, and the power cable connecting the power supply.
The common data cable types are: HDMI cable, VGA cable and DVI cable. There is also a DP cable for notebook!
This product is suitable for computer and automatic connection cable with rated voltage of 500V and below. K type B low density polyethylene (LDPE) with oxidation resistance is used for insulation of cable ground wire core. Polyethylene has high insulation resistance, good voltage resistance, small dielectric coefficient and small influence of dielectric loss temperature and variable frequency. It can not only meet the requirements of transmission performance, but also ensure the service life of the cable. One
In order to reduce the mutual crosstalk and external interference between loops, the cable adopts shielding structure. According to different occasions, the shielding requirements of cables are as follows: the combined shielding of twisted pair, the total shielding of cable composed of twisted pair, and the total shielding after the combined shielding of twisted pair.
Shielding materials include round copper wire, copper strip and aluminum / plastic composite belt. Shielding pair and shielding pair have good insulation performance. If there is potential difference between shielding pair and shielding pair, the transmission quality of signal will not be affected.
PC Cable
ShenZhen Antenk Electronics Co,Ltd , https://www.antenkelec.com