In the production of paints and inks, how to add powders has become a problem for many manufacturers, and manufacturers who suffer from artificial feeding and open production are not rare. In the production of paints and inks, if the problem of flying dust and solvent evaporation cannot be solved, the factory will be full of potential safety hazards, posing a great threat to the health of the workers and the surrounding environment.
At present, there is no shortage of technology-leading coatings and ink equipment manufacturers in the world. Many countries in the United States, Germany, France, Switzerland and other developed countries are leading the world in dispersion, mixing and grinding technologies. However, in the paint and ink equipment market in China, it is very rare for the paint and ink factory to fully consider and provide complete solutions. This has even led many large-scale factories to fall into awkward situation.
A considerable part of the paint and ink factories in China still adopts the method of manually feeding materials in the production workshops. Large-scale factory funds and technical strength are strong. Equipment divisions or similar departments have been set up. They have their own equipment engineers and can configure or modify their own equipment. One of the largest paint companies in China, Guangdong Huarun Paint Co., Ltd., released its own technological achievements in 2007. It mainly uses high-velocity, low-pressure, and low solid-to-gas ratio dilute phase pneumatic conveying technology. It mainly uses Roots blowers. Power source to achieve automatic feeding of powder. In the published technical data, the plant has to purge the bypass valve before and after each delivery. After each day of transportation, check and clean the tanks and piping. Flange connections are made at the easy-to-block places for easy maintenance. It should be said that the condition of use is not satisfactory. This phenomenon is also consistent with the test results of Fucheng Machinery. The examples of paint manufacturers making their own equipment reflect the demand of advanced manufacturers for closed and automated production, and also reflect the current status quo.
Gongyi Fucheng has been working hard to become a “provider of the overall solution.†The long-term problems that plagued paint and ink manufacturers have become problems that Gongyi Fucheng’s engineers hope to solve. After several years of technical development and trial production practices, Fucheng Machinery has established mature metering and conveying technologies for the addition of liquid raw materials. For the filling of finished products, China has developed the first fully automatic filling production line in China. Fucheng Machinery's patented “High-efficiency Coating Island†includes automatic feeding technology for liquids and powders, dispersion, basket grinding, paint adjustment, and automated filling technology. It has been adopted by many paint and ink factories in recent years.
For the automatic feed of powder, there have been equipment manufacturers tried to use negative pressure pneumatic conveying method, called "vacuum suction." This method has a shorter delivery distance, a smaller delivery volume, and is easier to clog. It can only be used in a few cases, in particular it cannot be used for the production of solvent-based coatings. This method has been adopted by some coating equipment manufacturers in recent years, but it still needs manual weighing. The powder plant must be placed near the production equipment. It is not a reasonable method.
Products produced by different factories are all different, and their output varies. The types and amounts of powders that need to be added are also different. In addition, the original layout of the factory building is not so easy to change. It is not acceptable for all factories to arrange a separate powder feed plant near the production workshop. In particular, the more advanced and large-scale paint and ink factories usually have many types of products, large output, large factory area, higher requirements for safety and environmental protection, and higher requirements on the stability of production. This requires equipment manufacturers to have a more comprehensive grasp of various powder conveying technologies and conveying equipment.
In recent years, Fucheng Machinery has applied the pressure-dense, dense-phase pneumatic conveying technology to the coating industry. Trial production has achieved very good results. In practical applications, stable delivery of many varieties, long distances, and large quantities is realized. Based on the mastery of this more mature and applicable technology, as well as the mastery of bucket elevators, screw conveyors and other equipment, Fucheng Machinery has formed a closed powder feed and feed solution for different factories. The situation provides different equipment configurations to provide possibilities for fully automated production.
Fucheng Machinery's powder delivery solution can be divided into the following five parts:
Feed and storage system
Store all kinds of packaged powder according to variety to their own silo
Distribution and Metering System
According to the formula, different types of powders are measured separately and stored in the sending tank in order to be conveyed.
Delivery and redistribution systems
Different types of powder are delivered separately and distributed to different reactors
Dust collection and recovery system
The protection of the receiving tank through the dust collector is communicated with the atmosphere, and dust protection is provided when the powder is added to the powder tank.
Automatic Control System
Taking PLC as the control core, mainly relying on pneumatic devices to operate the entire system
The above advantages are due in large part to the maturity and application of pneumatic conveying technology in Fucheng Machinery. Positive pressure dense phase pneumatic conveying technology is used in the coatings and inks industry. For more advanced plants, it can meet long distance, multi-variety, multi-delivery targets, and both large-batch and small-batch transmissions, in principle. It avoids clogging and residue and is a superior conveying technology.
Some paint manufacturers have taken some different attempts, such as positive pressure high-speed dilute phase pneumatic conveying using a Roots blower as a power source. Due to the high gas velocity and the small solid-gas ratio, the pipeline wear is also large. Due to large air consumption, dust removal at the receiving end is also more complicated. The principle of dilute phase pneumatic conveying is to rely on a high gas velocity that is higher than the sedimentation velocity of the powder so that the powder will not be deposited or blocked. However, in practical applications, the change of the gas velocity at the elbow and the reduced diameter is unavoidable, and the phenomenon of pipeline deposition is difficult to completely eliminate. This not only affects the stability of the equipment work, but also affects the measurement accuracy. Equipment engineers are forced to use flange connections in easy-to-deposit places for easy removal and cleaning. After metering at the delivery end, it is measured again at the receiving end. If blindly increasing the air volume of the Roots blower, there will be higher requirements for the pressure on the pipeline and the dust removal at the receiving end, which will also be detrimental to energy conservation.
The engineers of Fucheng Machinery have found through experiments and practical applications that positive-pressure dense-phase pneumatic conveying can well avoid the above problems. Because the dense-phase transportation principle does not require that the gas flow velocity is higher than the sedimentation velocity, there is no problem that the gas velocity is lower than the sedimentation velocity and clogging occurs. The dense phase conveying speed is only 6-12 m/s, and the pipe wear is far less than the dilute phase pneumatic conveying. The power of the entire system comes from air compressors, but the pressure is only a few hundred kPa, and the air compressors just provide power for pneumatic control. This transport method has created a transportation record of more than two kilometers, and it has long been a cost-effective, mature and effective solution to the hidden dangers of long-distance transport. If it is transported at a long distance, the possibility of jamming increases, and an automatic blow-off nozzle can be installed. Once the jam occurs, it can be automatically blown open without complicated maintenance. In general, the distance between the paint and ink powder warehouse and the production workshop is often not more than two kilometers, and the possibility of failure is even smaller. In practical applications, there has been no failure of pipe blocking.
In addition, for different sizes of powder packaging bags, a suitable unpacking and blanking device is designed, a metering device is set at a suitable location, and the setting of a level meter in a large-scale silo, and a bucket elevator and a belt type The use of conveyors and screw conveyors must be considered. The search for appropriate solutions to these problems and the mastery of the core pneumatic conveying technology have enabled Fucheng Machinery to better provide complete and mature services to the coatings and ink industries.
Welcome to OREMA's exclusive range of Front Terminal Batteries – the ideal choice for those who prioritize efficiency, space-saving design, and unwavering reliability in their power needs.
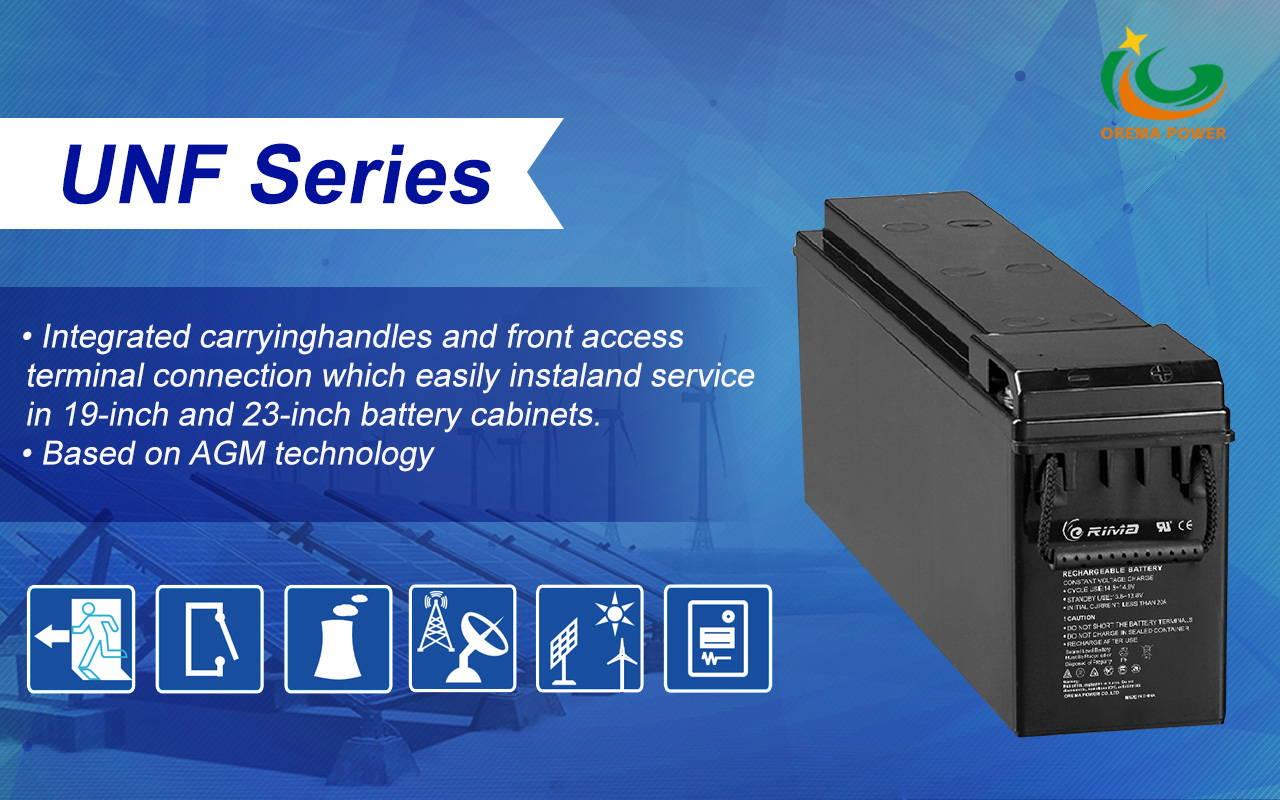
Innovative Design for Effortless Installation and Service
Our OREMA UNF series front terminal batteries redefine convenience with their integrated handles and accessible front terminal connections. Designed for seamless integration into both 19-inch and 23-inch battery cabinets, these batteries promise hassle-free installation and maintenance – a perfect fit for industrial, utility, and telecommunication settings.Advanced AGM Technology: Power, Performance, and Peace of Mind
At the heart of our OREMA UNF series lies the AGM (Absorbent Glass Mat) technology. This innovation encapsulates the electrolyte in glass fiber mats, offering enhanced performance and maintenance-free operation. Known for their high reliability and longevity, these batteries are the go-to solution for critical backup power requirements.Features of OREMA Front Terminal Storage Battery
Easy Installation & Space Efficiency: With front access terminals, our batteries simplify installation and servicing, saving you time and space.High Energy Density: Our batteries deliver superior performance while occupying less space, enhancing energy density.
Exceptional Discharging Ability: Thanks to radial grid design and tight assembly technology, these batteries excel in high-rate discharge performance.
Longer Float Service Life: Enjoy over 8 years of reliable service at 25°C, backed by unique corrosion-resistant grid alloy.
Maintenance-Free Operation: Our AGM technology ensures efficient gas recombination and eliminates the need for electrolyte maintenance.
Low Self Discharge: High purity raw materials reduce self-discharge, ensuring longevity.
Environmental & Nonpolluting: Our batteries feature Gas Recombination technology, preventing acid fog emissions.
Safe & Reliable: An efficient venting system releases excess gas and reseals valves, safeguarding against bursting.
Versatile Applications of OREMA Front Terminal AGM Battery
Our Front Terminal Batteries are designed for diverse applications including:19inch/23inch standard power supply cabinets
Communication Systems (Switches, Microwave Stations, Mobile Base Stations, Data Centers, Radio/Broadcasting Stations)
Special or LAN Power Supply Systems
Signal, Emergency Lighting, EPS & UPS Systems
Broadband, Electric Utility, Telecom, Central Office, Fire Alarms, and Security Systems
Specifications of the OREMA UNF series 12V Front Terminal Batteries:
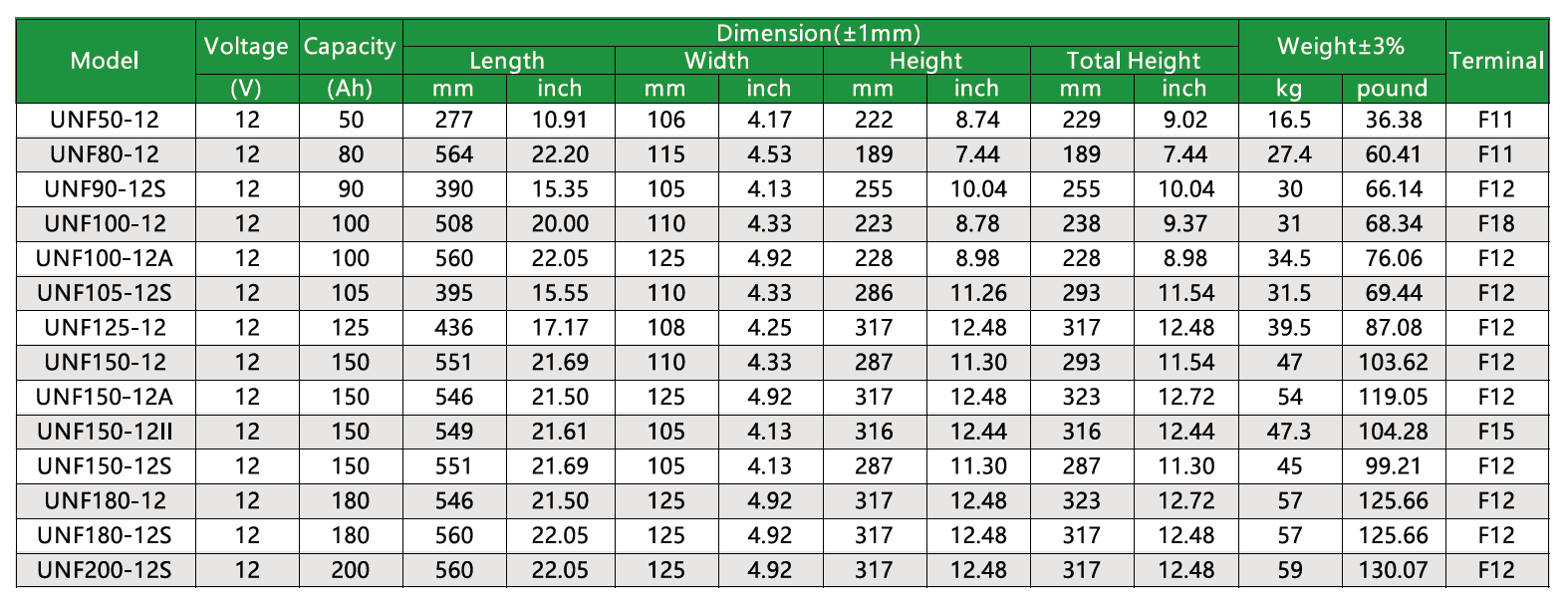
Tailored Solutions with OREMA's Expertise
With 20 years of innovation in sealed lead-acid battery manufacturing, OREMA stands as a rising star in the industry. Our commitment to quality is unwavering, as evidenced by our comprehensive quality management system. Embracing unity, growth, trust, and quality-first ethos, our team is dedicated to providing top-tier power solutions and personalized services. Meeting and exceeding customer expectations remains our perpetual goal.
Front Terminal Batteries,front terminal sla battery,front terminal storage battery,front terminal agm battery,12V front terminal batteries
OREMA POWER CO., LTD. , https://www.oremabattery.com